PCR plastic packaging is essential in today’s world due to the escalating plastic pollution crisis and its severe environmental impacts.
Since the 1950s, over 9 billion tons of plastic have been produced, yet only about 10% has been recycled. Due to their non-biodegradable nature, the remaining plastic persists in the environment for 500–1,000 years, contributing to severe plastic pollution.
The need for sustainable solutions is urgent. PCR plastic packaging helps to address this issue by recycling consumer waste into new products, reducing the amount of plastic that ends up in landfills or oceans.
This approach supports a circular economy, conserves resources, and minimizes waste, making it a crucial step towards a more sustainable future.
Introduction
What is PCR Plastic?
PCR plastic is made from waste plastic materials that have been discarded by consumers. It typically comes from plastic bottles, plastic wraps, and other discarded plastic items. After being collected, cleaned, and processed, it is transformed into usable plastic resin for manufacturing new plastic products.
Waste plastic materials can be water bottles, household product containers, post-industrial waste, soft drink bottles, plastic wraps and many more.
These materials are commonly found every day in our modern life and contribute significant plastic pollution.
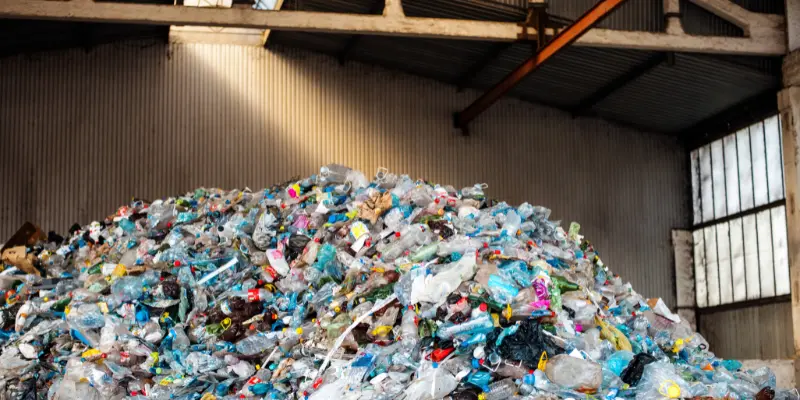
What is PIR Plastic?
PIR (Post-Industrial Recycled) plastic is made from plastic materials that are discarded during the manufacturing process of plastic products, rather than from post-consumer waste.
These plastics are often the off-cuts, trimmings, or scraps that are generated during the production of new plastic products, such as plastic sheets, bottles, or packaging materials.
Instead of being discarded as waste, these materials are collected, cleaned, and recycled back into usable plastic resin for creating new products.
PIR (Post-Industrial Recycled) plastic is generally considered more consistent in quality compared to PCR (Post-Consumer Recycled) plastic, since it comes from a controlled industrial environment and is less likely to contain contaminants like food residue or household chemicals.
This makes PIR (Post-Industrial Recycled) plastic an attractive option for manufacturers looking to produce sustainable products without compromising on quality.
Examples of PIR plastic materials include the excess plastic from injection molding, extrusion processes, and leftover plastic from product assembly lines.
The recycling process for PIR plastics typically involves sorting, cleaning, and melting the material to turn it into usable resin.
Both PCR and PIR plastics are important for a circular economy, where products are made with their recycling in mind. The goal is to reuse materials, reduce waste, and save natural resources.
Types of PCR Plastic?
Several types of plastic can be recycled and utilized in Post-Consumer Recycled (PCR) packaging, including:
- r-PET (Recycled Polyethylene Terephthalate)
- r-HDPE (Recycled High-Density Polyethylene)
- r-PP (Recycled Polypropylene)
- r-LDPE (Recycled Low-Density Polyethylene)
- r-PS (Recycled Polystyrene)
- r-PVC (Recycled Polyvinyl Chloride)
Which Plastics are Most Commonly Used for PCR Packaging?
PET (Polyethylene Terephthalate): It is one of the most widely used plastic for recycling processes, and it is often used in PCR products like, fleece jackets and water bottles.
HDPE (High-Density Polyethylene): It is also highly recyclable plastic and often used in PCR products like bottles and pipes.
PP (Polypropylene): It can be recycled, but less commonly used in PCR packaging. Yogurt containers are the example of PCR plastic.
Which Plastics are Less Commonly Used for PCR Packaging?
LDPE (Low-Density Polyethylene): LDPE is more challenging to recycle, and fewer recycling centers accept it because of contamination. However, it can also be used in PCR products like, plastic films, plastic bags and outdoor furniture.
PS (Polystyrene): PS is difficult to recycle, particularly if it is in Styrofoam. However, it can be processed into recycled products, like insulation pads.
PVC (Polyvinyl Chloride): PVC is technically recyclable but less commonly recycled due to concerns about chemical additives. It is typically not used as widely in PCR applications compared to PET or HDPE.
PET and HDPE are the most widely accepted and commonly used plastics for PCR applications due to their high recycling rates and versatile uses.
PP, LDPE, PS, and PVC are less frequently used for PCR products due to challenges in recycling process.
However, as recycling technologies improve (Chemical Recycling), more types of plastic can be used in PCR packaging.
How is PCR Plastic to be Made?
PCR (Post-Consumer Recycled) plastic can be made through two main types of recycling techniques: Mechanical Recycling and Chemical Recycling.
Here’s a detailed explanation of both recycling techniques:
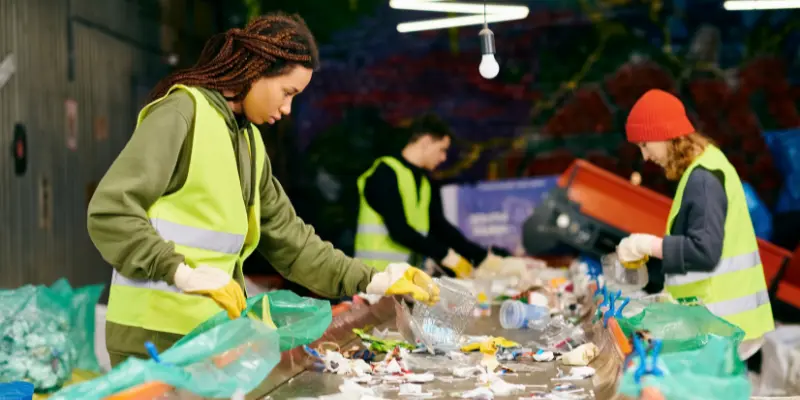
1. Mechanical Recycling of Plastic
Mechanical recycling is the most commonly used method for plastic recycling. It involves physically breaking down plastic waste into smaller pieces, cleaning it, and then reprocessing it to create new products.
Collection and Sorting
Post-consumer plastic waste is collected, sorted, and separated by means of their plastic category. Common materials like PET (Polyethylene Terephthalate) and HDPE (High-Density Polyethylene) are often separated and used for easy processing.
Cleaning and Shredding
The plastics are thoroughly cleaned or washed to remove contaminants such as food or chemical residue, labels, and adhesives. This cleaned plastic is then shredded into smaller pieces (flakes or pellets).
Melt and Extrusion
The plastic pieces are then melted at high temperatures and extruded into new shapes.
Forming New Products
The melted plastic is formed into plastic granules to make new products, such as plastic sheets, bottles, containers, films, or even plastic fibers for textiles.
Advantages
Cost-Effective: Mechanical recycling is often cheaper than chemical recycling since it uses less energy and fewer chemicals in processing.
Widespread: This method is well-established and has a large infrastructure across different countries.
Challenges
Quality Degradation: PCR plastic may lose some of its original properties during shredding and reheating. Over time, repeated mechanical recycling can lead to polymer degradation, reducing the strength, flexibility, appearance, and transparency of the material.
However, the extent of this degradation depends on the type of plastic, the recycling method used, and the number of recycling cycles.
Contamination Risks: Impurities from the previous use can contaminate the material during reheating, which may affect its purity and appearance.
This is one of the reasons why food and pharma packaging is not using PCR plastic.
Limited to Certain Plastics: Mechanical recycling works best with plastics like PET and HDPE. Some plastics, such as PVC blisters or multilayer packaging, are challenging to recycle mechanically.
2. Chemical Recycling of Plastic
Chemical recycling (also known as advanced recycling or feedstock recycling) is a more complex process that breaks down plastics into their basic chemical building blocks (monomers or raw materials).
This allows the plastic to be recycled indefinitely without quality degradation.
1. Depolymerization
Chemical recycling involves breaking down long polymer chains into their original monomer through chemical reactions.
This process can be done in different ways depending on the type of plastic being recycled.
Types of Depolymerization
Pyrolysis: It is also known as thermal cracking. In this process plastics are heated to high temperatures in the absence of oxygen, breaking them down into simpler molecules, which can then be refined into raw materials like oils or gases. These raw materials can be used to create new plastic or other chemicals.
Gasification: This involves partially oxidizing plastic waste at high temperatures to produce syngas (a mixture of hydrogen and carbon monoxide), which can then be used to create chemicals or fuels.
Hydrolysis: This involves breaking down plastics with water and enzymes. It is often used for specific plastics like PET and converts plastics into their monomers (e.g., terephthalic acid and ethylene glycol for PET) so that they can be purified and reused to make new plastic water bottles or other items.
Solvolysis: Similar to hydrolysis, but it uses solvents instead of water to break down plastics into their monomer.
2. Reformation
The monomers obtained from the chemical process can be refined and re-polymerized to create new plastic or other products, like fuel, and synthetic rubber.
Advantages
High-Quality Recycling: Chemical recycling can theoretically recover the original properties of the plastic, even from contaminated plastic waste or complex laminated plastic structures.
Versatility: It works on a wider range of plastics, including multilayer laminates, PVC, PS, and other non-recyclable plastics that can’t be processed by mechanical recycling.
Closed Loop Recycling: Chemical recycling has the potential for infinite recycling without degrading plastic quality.
Challenges
Energy Intensive: Chemical recycling requires more energy than mechanical recycling, especially for processes like pyrolysis or gasification, which can be a concern for its carbon footprint.
Cost: The technology is still developing, and the costs are currently high compared to mechanical recycling.
Chemical Pollution: It may generate by-products or pollutants that need to be managed to avoid environmental pollution.
Mechanical recycling is more widely used, cost-effective, and established, but it has limitations in material quality and is restricted to certain types of plastic and industry.
On the other hand, chemical recycling has the potential to address a wider range of plastics, including those that are difficult to recycle mechanically, and can yield higher-quality products, but it currently faces challenges related to cost, energy use, and carbon foot print.
Benefits of PCR Plastic Packaging
PCR Plastic packaging offers several benefits that contribute to a more sustainable future. Here’s an overview of the key advantages.
1. Reduces Plastic Waste
Prevents Landfill Overflow: By reusing plastic waste that would otherwise end up in landfills, PCR plastic packaging helps to keep plastic out of the waste stream.
Decreases Ocean Pollution: By reducing plastic waste in oceans, PCR plastic packaging helps to mitigate the negative impact of plastic on marine animals, which often ingest or get entangled in plastic waste.
2. Conserves Natural Resources
Less Dependence on Virgin Materials: PCR plastic packaging reduces the need to extract and process new petroleum or natural gas for creating plastic. For example: Oil and Natural Gas Saving.
Circular Economy Contribution: By reusing plastic waste, PCR plastic packaging supports a circular economy, ensuring that plastic is continuously reused rather than discarded. This means resources are used multiple times, contributing to long-term sustainability.
3. Lower Energy Consumption
Energy Savings: Recycling plastic uses significantly less energy than producing new plastic from virgin raw materials. For example, making plastic from recycled PET (r-PET) can save up to 60-80% of the energy compared to producing plastic from virgin PET.
Reduced Carbon Emissions: Because of less energy consumption, carbon emissions are also reduced, making it a more environmentally friendly option. For example, producing plastic bottle from r-PET emit about 40% less carbon than producing plastic bottle from virgin PET polymer.
4. Economic Benefits
While producing PCR plastic can sometimes be more expensive than using virgin plastic, the cost savings from energy reduction and resource conservation can offset those expenses in the long term.
5. Consumer Appeal and Brand Value
Businesses that use PCR plastic in their product packaging can appeal to eco-conscious consumers, who are increasingly seeking sustainable products.
6. Reduced Manufacturing Timeline
Creating PCR plastic is faster and less complex than producing virgin plastic, as it skips the extraction and refining of crude oil and natural gases, and avoids many energy-intensive steps like polymerization.
7. Lower Waste Management Cost
If plastic waste is reused instead of discarded, the time and cost associated with cleaning landfills, oceans, or waterways can be reduced. Less plastic in oceans means less time and money spent on environmental cleanup projects.
Challenges and Limitations of PCR Plastic Packaging
While PCR (Post-Consumer Recycled) Plastic offers significant benefits, there are several challenges and limitations associated with its use, particularly around quality, safety, and strength.
Here’s an overview of these challenges, including concerns about migration and leachability.
1. Quality and Consistency
Inconsistent Material Quality: PCR plastic often varies in quality because it is made from used plastic items or waste plastics having different usage histories.
The source of plastic items (e.g., food packaging, pharma packaging, chemical packaging, cosmetic packaging, industrial products, etc.) can affect its purity and suitability for reuse.
Color and Appearance: PCR plastic may have a different color than virgin plastic, and the final product might not have the desired aesthetic look.
Surface Defects: Imperfections in recycled plastic may appear more frequently, requiring additional treatment or modification, which can increase costs.
2. Contamination and Impurities
Contamination During Recycling: PCR plastic can be contaminated with residues from food, chemicals, cosmetics, pharma, or other materials, which can affect the quality of the final product.
For example, if a food container is not properly cleaned before recycling, traces of food can remain in the final plastic.
Harmful Additives: Some plastics contain additives (e.g., colorants, flame retardants, stabilizers) that might not break down or be removed during recycling, which are affecting the safety and performance of PCR plastic.
3. Migration and Leachability Risk
PCR plastics can pose health risks due to the potential transfer of harmful chemicals from the packaging into food, medicine, beverages, or cosmetics.
Over time, substances like phthalates, Bisphenol A (BPA), and antimony (used in PET production) may leach into consumables, raising concerns about toxicity, carcinogenicity, and endocrine disruption.
This risk is especially high in packaging that directly touches food, medicines, or cosmetics, so strict rules are in place to keep consumers safe.
Inadequate recycling processes can leave behind contaminants, further increasing the likelihood of chemical migration and environmental pollution.
4. Limited Recycling Capacity
Not all plastics are equally recyclable. Low-density polyethylene (LDPE), polystyrene (PS), and polyvinyl chloride (PVC) are harder to recycle effectively, meaning only certain types of plastic, like PET and HDPE, are commonly used for PCR products.
In many parts of the world, waste management systems are not sufficiently developed to ensure that the right types of plastic are being properly recycled.
5. Cost Barriers
The cost of manufacturing PCR plastic can sometimes be higher than using virgin plastic.
This is particularly true if the collection, sorting, and cleaning processes are inefficient, or if the demand for high-quality PCR plastic exceeds the available supply.
In some cases, companies may find it more cost-effective to use virgin plastic rather than investing in the infrastructure and technologies needed for recycling.
6. Public Perception and Acceptance
Consumers may have concerns about the safety and quality of products made from PCR plastic, especially when it comes to food and pharmaceutical packaging.
While PCR plastic offers significant environmental and economic benefits, challenges such as material quality, contamination, and migration of chemicals must be addressed to ensure its continued success.
Applications for PCR Plastic Packaging
Post-Consumer Recycled (PCR) plastic is being adopted across several industries, but its use is more prevalent in some sectors than others.
Below is a breakdown of industries that are actively using PCR plastic and those that aren’t.
Industries Actively Using PCR Plastic
1. Food & Beverage Industry
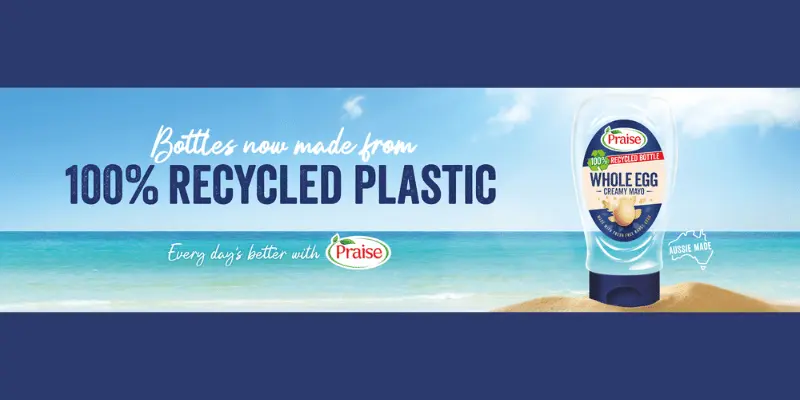
The food and beverage industry is one of the largest users of PCR plastic, especially for packaging.
For example, Goodman Fielder has adopted recycled PET (rPET) bottles for its food packaging, reducing reliance on virgin plastic and supporting a circular economy.
By repurposing post-consumer plastic waste into new bottles, the company minimizes environmental impact and promotes sustainability in the packaging industry.
Another example, companies like Coca-Cola and PepsiCo are using PCR plastic for their bottles and packaging.
Coca-Cola’s “World Without Waste” initiative aims to collect and recycle the same number of bottles and cans it sells by 2030, using recycled plastic to help achieve this goal.
2. Cosmetics and Personal Care
Many cosmetic and personal care brands are using PCR plastic for bottles, jars, tubes, and other packaging items.
For example, brands like L’Oréal and Unilever have incorporated recycled plastic into their product packaging.
3. Consumer Electronics
In the electronics sector, brands like Apple and Google have started incorporating PCR plastic in some parts of their packaging, such as boxes, and in the production of certain plastic components.
4. Automotive Industry
The automotive industry has started to use PCR plastic for certain non-structural parts of vehicles, including interior panels, bumpers, and trim components.
5. Apparel and Textile
The fashion industry, especially companies making activewear and outerwear, is using PCR plastic in the form of recycled polyester (r-PET).
Brands like Patagonia and Nike have pioneered the use of PCR plastic in their clothing and footwear.
6. Building and Construction
The construction industry is also exploring the use of PCR plastic for insulation materials, pipes, tiles, and recycled plastic boards for furniture or other structural applications.
Industries With Limited Use of PCR Plastic
1. Pharmaceutical Industry
The pharmaceutical sector generally avoids the use of PCR plastic in primary packaging or medical devices.
Reason for Limited Use
Sterility and Safety: The pharmaceutical industry has stringent safety and sterility standards. Packaging that comes into direct contact with medicines must meet certain standards, and PCR plastic does not always meet these safety standards.
Risk of Contamination: PCR plastic, especially when sourced from mixed consumer waste, can carry risks of contamination with toxic chemicals like phthalates, BPA, and heavy metals that could affect the quality and safety standards of pharmaceutical products.
2. Medical Devices and Healthcare
Medical devices, like syringes, surgical tools, and implantable devices, rarely use PCR plastic.
Reason for Limited Use
Material Purity: Medical devices need to be made from materials having high-quality performance to ensure patient safety. PCR plastic often lacks in quality and consistency if it is made from mechanical recycling.
Regulation and Certification: The medical field requires extensive testing and certification for materials, and PCR plastic may not meet the rigorous standards for certain types of medical products.
How Can We Use PCR Plastic in Food and Pharma Packaging?
Combining PCR plastic with virgin material for food and pharmaceutical packaging can be an effective strategy to reduce contamination risks while still promoting sustainability.
This approach allows companies to use varying percentages of PCR plastic (e.g., 30%, 50%, 70%, or even 100%) depending on the specific requirements of the product and its packaging, while still maintaining high safety standards for sensitive applications.
Percentage of PCR Plastic in Packaging
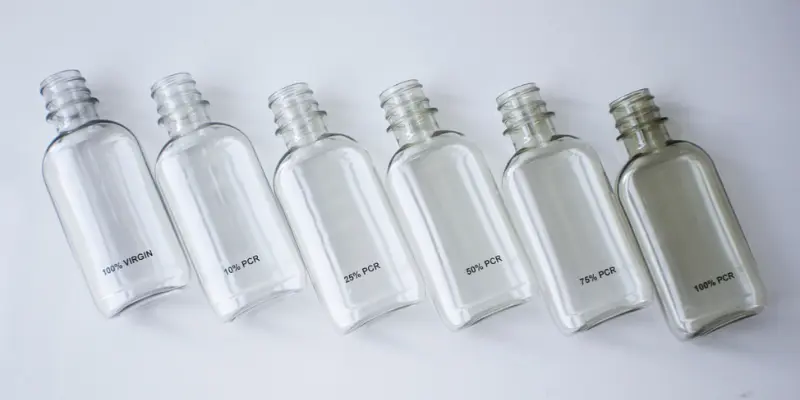
30% PCR Plastic: This lower percentage of PCR content is ideal for applications where the focus is on starting the transition toward sustainability while still prioritizing the safety and quality of the product. It can be used for outer layers or non-direct product contact areas.
50% PCR Plastic: A balanced approach where sustainability is significantly enhanced while still ensuring compliance with safety standards. This could be applied in packaging where the safety risks are moderate, such as in secondary packaging or where there is less direct contact with the product.
70% PCR Plastic: This higher percentage demonstrates a strong commitment to sustainability while maintaining the necessary performance in terms of safety and functionality. It’s suitable for products that do not require a fully virgin material contact surface but still require strict control of contaminants.
100% PCR Plastic: In certain applications, where regulations and technology permit, packaging could be made from 100% PCR plastic. This would be more common for packaging that does not directly touch the food or pharmaceutical product but still requires robust protection.
However, 100% PCR packaging needs to undergo rigorous testing to ensure no migration or contamination risks from the PCR content.
Product Contact with Virgin Material
Virgin material would be used for the part of the packaging that comes into direct contact with the food or pharmaceutical product. This ensures that there is no risk of contamination from harmful chemicals, toxins, or migration of substances from PCR plastic.
The outer layer of the packaging can be made from PCR plastic, offering a reduced environmental footprint while maintaining safety standards for the internal contents. The percentage of PCR content would be determined by regulatory guidelines, safety tests, and the functional requirements of the packaging.
Examples of Food Packaging
Yogurt Containers: The inner layer, which directly contacts the yogurt, can be made from virgin plastic (e.g., virgin PET or PP) to ensure safety, while the outer layer can be made from PCR plastic.
The PCR content can range from 30% to 70%, depending on the level of sustainability desired without compromising food safety.
Snack Bags: The inner lining, which holds the food, can use virgin plastic for better moisture and oxygen barrier properties, while the outer layer of the bag can use PCR plastic, with the percentage of PCR plastic ranging from 50% to 100% based on the specific application.
Examples of Pharmaceutical Packaging
Bottle Packs for Tablets: The inner portion of the bottle, in direct contact with the tablets, can be made from virgin plastic to ensure there are no migration risks. The outer layer, which is not in direct contact with the product, can use PCR plastic.
The PCR content here could range from 30% to 70%, depending on the packaging design and safety considerations.
Blister Packs: The base film, such as PVC, can be laminated with both virgin plastic and PCR plastic. The virgin plastic layer will remain in contact with the tablets to meet safety standards, while the PCR plastic layer will be on the outside of the blister pack.
The percentage of PCR used in the outer layer can vary from 50% to 100%, depending on the product’s packaging requirements.
Factors to be Considered While Using PCR Plastic
When considering the use of PCR (Post-Consumer Recycled) Plastic, several factors need to be assessed to ensure its effectiveness, safety, and suitability for specific applications.
1. Material Compatibility
Application Suitability: Not all types of PCR plastic are suitable for every application. For example, PCR plastic used in food and pharma packaging needs to meet safety regulations to avoid contamination from migration of harmful substances.
Mechanical Properties: The mechanical strength, flexibility, and durability of PCR plastic may differ from virgin plastic. It is essential to test whether the PCR plastic can meet the requirements of the product, such as strength, transparency, or resistance to wear and tear.
2. Safety and Contamination Risk
Chemical Migration: PCR plastic may carry chemical residues or contaminants from the previous usage of the material, which could migrate into food, beverages, medicines, or cosmetics.
Testing for Migration: Ensure the PCR plastic has been tested for harmful chemical migration, such as phthalates, BPA, or flame retardants, to ensure it meets safety standards. Migration test, and extractable-leachable test can be performed.
Leachability: Ensure the PCR plastic has no leachable substances that could negatively affect the quality or safety of the product.
3. Compliance with Regulatory Standards
Check whether the PCR plastic used in products complies with recycling standards like those set by organizations such as ISO 14021 (Environmental Labels and Declarations), EuCertPlast, or similar certifications that ensure the recycled content meets necessary environmental and quality benchmarks.
4. Amount and Traceability of PCR Content
It’s crucial to know the percentage of post-consumer recycled (PCR) plastic used in a product or packaging and ensure its traceability to verify the origin and authenticity of the recycled materials.
This includes confirming that the recycled plastic is sourced responsibly from various origins like food packaging, chemical packaging, or ocean plastic, with transparent tracking systems in place to confirm the amount of post-consumer content used.
5. Quality Control and Consistency
Inconsistent Quality: PCR plastic often has varied quality because it is made from recycled waste, which can vary based on the source. This can result in color inconsistency, physical defects, or differences in performance.
Testing: Perform quality assurance tests to ensure the final product made from PCR plastic meets the required specifications for appearance, strength, durability, and performance.
6. Cost Implications
While using PCR plastic may reduce raw material costs in some cases, the cost of processing, sorting, cleaning, and testing can be higher than using virgin plastic, especially when material quality is variable.
Ensure that the economic benefits align with business goals.
Future Innovation
The future of PCR (Post-Consumer Recycled) plastic looks promising, but it faces several challenges in terms of scalability, quality, and cost-efficiency.
The increasing emphasis on sustainability, circular economy, and plastic waste reduction is pushing industries, governments, and consumers to embrace PCR plastic packaging.
However, for it to work effectively in the long term, significant advancements and adaptations in technology, infrastructure, and market demand are required.
Technological Advancements
AI-Driven Sorting for Mechanical Recycling: Advances in AI-driven waste management systems can significantly improve the sorting process, leading to higher-quality PCR plastic with less contamination.
These systems can accurately identify and separate different types of plastics, ensuring that the recycled material is purer and more suitable for producing high-quality PCR plastic.
Chemical Recycling: This technology breaks down plastics into their basic monomers without degrading the quality of the plastic.
The resulting PCR plastic from chemical recycling is of such high purity that it can be used in food and pharmaceutical applications, addressing the stringent quality requirements of these industries.
Conclusion
PCR plastic packaging plays a crucial role in reducing plastic waste and promoting a circular economy by giving used plastics a second life. While it offers significant environmental benefits, such as lowering carbon footprints and reducing reliance on virgin plastics, challenges like quality, contamination, chemical migration, and mechanical degradation must be carefully managed. Industries are continuously improving recycling technologies and regulatory standards to enhance the safety and performance of PCR plastics, especially for food and pharmaceutical applications.
As businesses and consumers embrace sustainable choices, PCR plastic remains a vital step toward a greener future, balancing innovation with environmental responsibility.
If you have any points or questions that need to be addressed, feel free to leave a comment. I will research and include them in future updates.
Frequently Asked Questions
Yes, PCR plastic can be recycled. It is made from plastic waste that has already been used and discarded by consumers. After being collected, cleaned, and processed, PCR plastic can be melted down and turned into new products. However, like all plastics, its recyclability depends on factors such as the type of plastic, its contamination level, and the recycling technology available. With proper recycling systems in place, PCR plastic can be reused multiple times, helping to reduce waste and conserve resources.
No, PCR plastic is not biodegradable. Like other types of plastic, PCR plastic is made from synthetic materials that do not break down naturally in the environment. While recycling PCR plastic helps reduce waste and conserve resources, it does not decompose on its own like organic materials. It remains in the environment unless properly recycled or disposed of through other waste management methods.
There is no universal logo for PCR plastic. However, products made from PCR plastic often feature the recycling triangle symbol with a number or labels like “Post-Consumer Recycled” to indicate the use of recycled materials. Brands may also have their own logos to highlight PCR plastic use.
In short, yes—but it will depend on how the challenges are addressed. The demand for PCR plastic is set to increase, driven by regulations, consumer preferences, and industry commitments to sustainability.