Bamboo clothing is trending now in the fashion industry because of its eco-friendly characteristics, comfort, and sustainability. The market for bamboo clothing is growing and growing due to these unique features.
Derived from bamboo plants, this ecofriendly fabric is well-known for its softness, breathability, UV protection, moisture wicking capability, moisture absorption, permeability, pleasant tactile sensation, excellent dye-ability and natural antibacterial properties, making it a preferred choice for sensitive skin.
In today’s world, we are facing many challenges like economic troubles, environmental pollution, climate change and global warming. So, consumers are now becoming more conscious of their carbon footprint and are actively searching out sustainable clothing fabrics that are less harmful to humans and the environment.
By developing bamboo as a resource, we can produce eco-friendly and sustainable products to protect our planet for future generations and help to mitigate some issues what we face today.
Table of Contents
Introduction
The fashion and textile industry are creating huge environmental pollution through its manufacturing process. From extracting fibers to making clothes, every step in the manufacturing process has a negative impact on the environment.
The demand for new styles having less prices has led to fast fashion, which is making lots of low-quality clothes and throwing them away quickly.
The production of other textiles, especially synthetic fibers like polyester, nylon, rayon, acrylic, convectional cotton, and spandex are energy-intensive and heavily depend on fossil fuels, leading to emission of greenhouse gases.
1. Polyester: Made from petroleum, polyester production is highly energy-intensive and releases significant greenhouse gases. It also creates microplastics during washing, which pollute water bodies.
2. Nylon: Also derived from petroleum, nylon production generates nitrous oxide, a potent greenhouse gas. Nitrous oxide has a global warming potential (GWP) of approximately 298 times that of CO₂ over a 100-year period.
The process is energy-intensive, and the material is not biodegradable, contributing to long-term environmental pollution and degradation.
3. Rayon (Viscose): Though derived from natural cellulose, the production of rayon involves chemicals like carbon disulfide (CS2), sodium hydroxide (NaOH) and sulfuric acid (H2SO4), which can be toxic and harmful to factory workers and the environment. The process is also energy and water intensive.
Moreover, the recovery rate of carbon disulfide in most industries is only about 50%. Additionally, sodium hydroxide and sulfuric acid are also considered potentially hazardous chemicals.
4. Acrylic: Similar to polyester and nylon, acrylic is made from petroleum. Its production is energy-intensive and releases harmful emissions, including volatile organic compounds (VOCs).
5. Conventional Cotton: While a natural fiber, conventional cotton farming uses large amounts of water, pesticides, and synthetic fertilizers, leading to soil degradation, water pollution, and significant energy consumption in irrigation and processing.
6. Spandex (Lycra): This synthetic fiber is derived from polyurethane and involves energy-intensive processes. The production releases harmful emissions and the material is not biodegradable.
Because of the manufacturing process and nature of raw material, these fabrics are degrading the environment continuously and raising the need for more sustainable alternatives in textile industry.
By choosing bamboo fabrics, the fashion industry can significantly reduce its carbon footprint.
Cultivation of Bamboo and Its Environmental Benefits
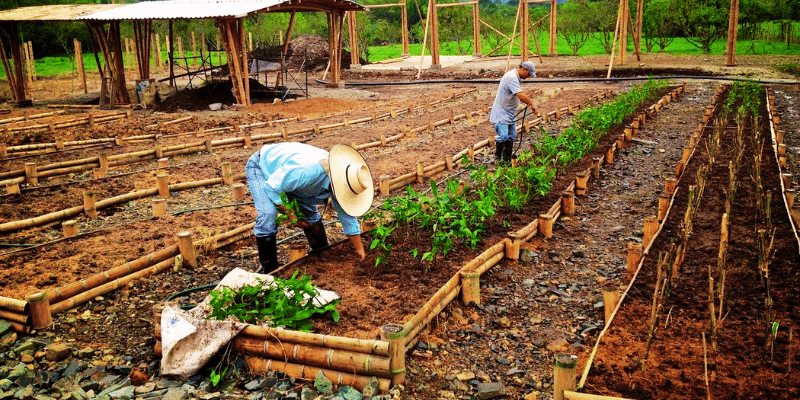
Bamboo’s sustainability is increased by cultivating the plant and utilizing all its parts. Apart from clothing, mature bamboo culms can also be used in construction and furniture. Immature bamboo shoots serve as food and are used in traditional medicine for various health benefits, including antioxidants, anti-aging properties, improved digestion, and more.
1. Rapid Growth
Bamboo is one of the fastest-growing plants in the world, capable of growing up to 32 inches per day.
While a forest tree takes about 60 years to re-grow after cutting, bamboo plants only take 2-3 years to grow back. This rapid growth rate of bamboo allows for frequent harvesting without the need of replanting.
2. Low Water Usage
Bamboo requires less amount of water as compared to water intensive crops like cotton. It can grow with natural rainfall, which reduces the need for irrigation. It is very beneficial for water scarcity regions, where water is limited for agriculture.
3. Minimal Pesticides and Fertilizers
Bamboo is naturally resistant to pests and diseases because of its bio-agent called Bamboo Kun, which reduce the need for pesticides and fertilizers that can harm the environment.
While pesticides are designed to control pests and weeds, they can also harm beneficial organisms in the soil such as earthworms, mycorrhizal fungi and Rhizobium bacteria. These beneficial organisms play crucial roles in maintaining soil structure and its health.
Excessive use of fertilizers can lead to imbalance of nitrogen and phosphorus in soil. This imbalance can alter the soil pH and reduce soil fertility over time.
4. Carbon Sequestration or Carbon Absorption
Bamboo forests are highly effective to absorb carbon dioxide and playing a very important role in mitigating climate change. Bamboo plants absorb more CO2 and release 35% more oxygen than equivalent stands of trees.
This makes bamboo cultivation an effective strategy in combating climate change. By sequestering large amounts of carbon, bamboo helps to reduce the overall concentration of greenhouse gases in the atmosphere, mitigating the effects of global warming.
The carbon sequestration rate for Moso bamboo (Phyllostachys edulis) can vary based on factors like age, management practices, and environmental conditions.
Generally, recent studies suggest rates ranging from approximately 5 to 13 tCO2/ha/yr and can be higher in well-managed forests.
5. Biodegradability
Bamboo is biodegradable, which breaks down naturally and enriches the soil.
Processing of Bamboo into Fabric
Manufacturing process of bamboo into clothing material involves two primary methods: mechanical processing and chemical processing. However, other methods are also used for bamboo clothing, such as retting processing and charcoal processing.
The chemical process can be divided into two types. One is like making rayon, where bamboo is broken down by strong chemicals and then spun into fibers.
The other type is like making Lyocell fibers, where closed-loop system is used.
The extraction method for the fiber plays a crucial role in determining the quality of resulting clothing fabrics.
Retting or Degumming Processing
Retting in the bamboo manufacturing process is a technique used to separate fibers from the bamboo stems.
It involves breaking down the pectin that binds the fibers together with plant tissue. This can be done through different techniques or methods, including:
1. Dew Retting
Bamboo stems are spread out in fields to expose them to dew and natural microbes. Over the time, these microbes break down the pectin, allowing the fibers to be separated from the plant material.
2. Enzymatic Retting
Pectin-degrading enzymes (pectinases) are applied to the bamboo stems in a controlled environment, such as a bioreactor. These enzymes specifically target and break down the pectin, facilitating the separation of fibers.
3. Water Retting
Bamboo stems are submerged in water, such as ponds, rivers, or tanks. Anaerobic bacteria present in the water release enzymes that break down the pectin for fiber separation.
4. Bio-Retting
This method uses natural processes similar to dew retting but is controlled to ensure consistent fiber quality. It relies on naturally occurring microbes and enzymes to break down the pectin for fiber separation.
5. Mechanical Retting
In this method, mechanical processes like crushing or beating are used to physically break apart the bamboo stems to separate the fibers. This can be less precise and may result in variable fiber lengths.
6. Chemical Retting
Acidic or alkaline solutions, such as sodium hydroxide (NaOH) or hydrochloric acid (HCl), are applied to the bamboo stems to dissolve the pectin and facilitate fiber separation. This method is efficient but requires careful handling of chemicals.
Advantages of Retting Processing
1. Retting is a natural process that uses microbes or enzymes to break down pectin, making it environmentally friendly.
2. Depending on the method used, retting can preserve the strength and integrity of natural fibers.
3. Excellent moisture wicking ability because of its micro-gaps and micro-holes in the fiber.
4. Fibers produced by this method can retain all their original properties.
Disadvantages of Retting Processing
1. Retting can be a slow process, requiring days to weeks for microbes or enzymes to break down the pectin adequately.
2. The quality of fibers obtained through retting can vary due to various factors such as environmental conditions and microbial activity.
3. Water retting can lead to pollution if not managed properly, while chemical retting may involve hazardous chemicals.
4. Achieving consistent fiber quality across batches can be challenging, especially with natural retting methods.
Mechanical Processing
The fiber extracted through mechanical processes is often referred as “natural” or “original” bamboo fiber.
This process is more environmentally friendly and able to retain its natural properties in resulting clothing fabric, but it is less common due to its higher cost and lower efficiency compared to chemical processing.
Here’s a step-by-step overview:
1. Harvesting
Mature bamboo stalks are harvested and cut into smaller pieces.
2. Crushing
The bamboo pieces are then crushed into a pulp. This is typically done by using a mechanical crusher or a similar machine.
3. Natural Enzyme Treatment
The crushed bamboo pulp is treated with natural enzymes that help to separate fibrous material from other culm parts. These enzymes are eco-friendly and help in softening the bamboo fibers.
4. Combing
The resulting fibrous material is then combed out to separate the long fibers. This process helps in aligning the fibers, making them suitable for spinning.
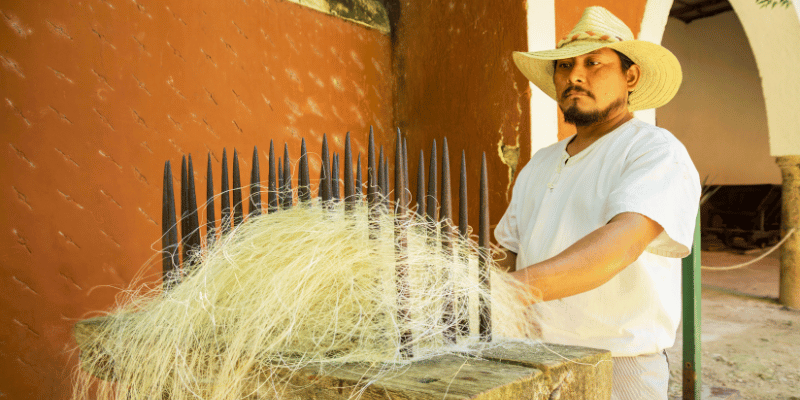
5. Spinning
The combed fibers are spun into yarn using traditional spinning methods. This yarn becomes woven or knitted into clothing material.
6. Finishing
The fabric undergoes finishing processes such as dyeing, which can also be done using natural dyes to maintain the sustainability aspect.
Bamboo textiles made from mechanically process are rough and stiff, but represent excellent properties, such as breathability, comfortable to wear, moisture wicking ability, and antibacterial properties.
Additionally, fiber processed mechanically tends to have greater strength and durability than chemically processed fiber. This difference arises from the physical changes that occur during chemical processing, which can alter the fiber’s molecular structure.
Advantages of Mechanical Processing
1. Environmentally friendly due to the absence of toxic chemicals.
2. Produces strong and durable fibers.
3. The resulting green fabric retains more of the natural qualities of bamboo, such as
breathability, hypoallergenic, UV protection, antifungal and antibacterial
properties.
Disadvantages of Mechanical Processing
1. More labor-intensive and time-consuming.
2. The yield of bamboo fiber is lower, making it more expensive.
3. The resulting bamboo fabric, often called bamboo linen, can be less soft as compared to chemically processed bamboo fabric.
Chemical Processing
On comparison to mechanical processing, chemical procedures require less expensive equipment, consume less energy, and provide greater control over fiber qualities.
There are two types of chemical processing, rayon process and closed-loop process.
Rayon Process or Viscose Process
It is most widely used in commercial production of bamboo clothing materials, which involves break down of bamboo fibers using chemicals like sodium hydroxide and carbon disulfide for creating a viscose solution, which is then spun into fibers.
Despite its effectiveness, this process can be harmful to the environment if not managed properly. However, closed-loop production processes can be used to mitigate these impacts.
1. Harvesting
Similar to mechanical processing, mature bamboo stalks are harvested and cut into smaller pieces.
2. Steaming and Crushing
The bamboo pieces are steamed and crushed to soften them, making it easy for further processing.
3. Chemical Treatment
The crushed bamboo is soaked in a solution of 18 % NaOH at 20–25 °C for 1–3 h to form alkali cellulose. Sodium hydroxide is used to break down the lignin and hemicellulose that bind the cellulose fibers.
This chemical treatment dissolves the bamboo cellulose and creates a viscous solution.
The bamboo alkali cellulose is pressed to remove excess NaOH solution and then allowed to dry for 24 hours.
After that, carbon disulfide (CS2) is added to the bamboo alkali cellulose to sulfurize the compound. Finally, the remaining CS2 is evaporated through decompression and resulting in sodium xanthogenate. This process is known as sulphurisation and xanthation.
A diluted NaOH solution is added to the cellulose sodium xanthogenate, which helps to dissolve it into a viscose solution containing approximately 5% NaOH and 7–15% bamboo fiber cellulose.
4. Spinning
The viscous solution is then forced through spinnerets (fine holes) to form threads.
As the solution passes through the spinnerets, it solidifies to form regenerated cellulose fibers. These fibers are then spun into yarn.
5. Neutralizing and Washing
The fibers are soaked in a sulfuric acid (H2SO4) bath to neutralize any remaining chemicals.
They are then thoroughly washed to remove residual chemicals and impurities.
6. Drying and Finishing
The fibers are dried and undergo finishing processes such as dyeing and softening to enhance the texture and appearance of the final bamboo fabric.
Closed-Loop Process or Lyocell Process
Closed-loop or lyocell process is considered as more greener solution for generating bamboo clothing fabric.
1. Harvesting
Similar to mechanical processing, mature bamboo stalks are harvested and cut into smaller pieces.
2. Steaming and Crushing
The bamboo pieces are steamed and crushed to soften them, making it easier to process further.
3. Chemical Treatment
In the Lyocell process for bamboo fiber manufacturing, N-methylmorpholine-N-oxide (NMNO) is used to dissolve bamboo cellulose into a viscose solution.
NMNO, a weak alkaline and surfactant, helps to break down the cellulose structure.
The solution is then forced through spinnerets into a hardening bath, typically containing H2O2 and an alcohol like methanol or ethanol, which solidifies the viscose into bamboo cellulose fibers.
These regenerated fibers are then spun into yarns.
The Lyocell process significantly reduces the environmental impact compared to the traditional viscose method, making it more eco-friendly, as the amine oxides used are non-toxic to humans.
This closed-loop process captures and recycles 99.5% of the chemicals, creating virtually no waste and only minimal emissions.
As a result, it is considered one of the most environmentally friendly methods for producing regenerated fibers, with bamboo fibers made this way labeled as Lyocell.
Advantages of Chemical Processing
1. Efficient and cost-effective method for producing soft, smooth, and highly versatile
fabric.
2. The resulting bamboo viscose fabric is soft, smooth, and has excellent drapability.
Disadvantages of Chemical Processing
1. Environmental concerns due to the use of harmful chemicals like sodium
hydroxide and carbon disulfide.
2. Potential for chemical waste and pollution if not managed properly.
Bamboo Charcoal Fiber Processing
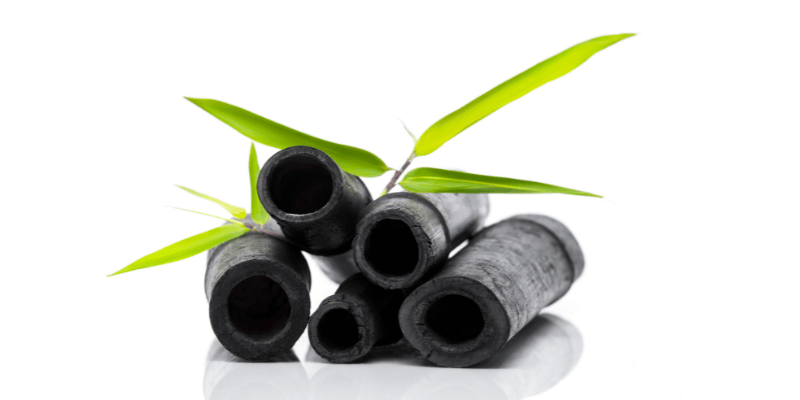
The manufacturing process of bamboo charcoal fiber typically involves the following steps:
1. Raw Material Preparation
Bamboo charcoal fiber starts with bamboo plants, specifically the parts rich in cellulose and lignin. These parts are harvested and processed to extract cellulose.
2. Carbonization
The bamboo materials undergo a process called carbonization, where they are heated to high temperatures (often around 800-1000°C) in the absence of oxygen. This process converts the bamboo into bamboo charcoal.
3. Activation
After carbonization, the bamboo charcoal is activated. Activation involves treating the charcoal with oxidizing gases or steam at high temperatures. This step creates pores and increases the surface area of the charcoal, which enhances its adsorption capabilities.
4. Mechanical Processing
The activated bamboo charcoal is then mechanically processed into fibers. This involves shredding or grinding the charcoal into small particles.
5. Spinning
The ground bamboo charcoal particles are spun into fibers using either a wet spinning or dry spinning process, depending on the desired properties of the final fiber.
6. Yarn Production
The spun bamboo charcoal fibers are then spun into yarns, which can be further processed into fabrics or used for other applications.
7. Finishing
The bamboo charcoal fibers or fabrics may undergo finishing processes to enhance their properties, such as softening, dyeing, or applying additional treatments for specific functionalities.
This process results in bamboo charcoal fibers that are known for their unique properties, including moisture-wicking, odor control, and potential health benefits due to their antibacterial and antimicrobial properties.
Benefits of Bamboo Clothing
1. Antibacterial Property
Bamboo possesses inherent antibacterial property due to its natural bioagent known as Bamboo Kun. Remarkably, this property is retained even after processing and washing of cloth, making bamboo fabric highly beneficial for infant’s wear, sportswear and activewear, as it helps to maintain freshness and hygiene.
Because of this unique antibacterial property, bamboo clothing effectively removes bacteria and mildew, unlike other cellulosic fabrics that can promote their growth, leading to unpleasant odors and potential fiber degradation.
It’s true that bamboo’s antibacterial properties are partly due to compounds like chlorophyll and sodium copper chlorophyllin, which act as antibiotics and deodorizers. These elements contribute to bamboo’s natural resistance to bacteria.
Additionally, the lack of free electrons in bamboo fibers makes the fabric antistatic, making it to fit comfortably against the skin and drape smoothly without clinging.
2. Antifungal Property
Protein dendrocin found in bamboo exhibits remarkable fungal resistance. This property contributes to bamboo’s natural ability to resist fungal growth.
Bamboo’s antifungal property is very useful during the monsoon season where the humid atmosphere creates ideal conditions for fungal growth. This natural resistance helps to keep bamboo products clean and free from fungi.
This property is very beneficial in bamboo diapers, where the chance of fungus growth is more.
3. Odor Removal Property
The natural antimicrobial agents within bamboo fibers help to inhibit the growth of odor-causing bacteria. As a result, bamboo fabric can effectively neutralize unpleasant smells, keeping clothing and other products fresh even after extended use.
This makes bamboo an excellent choice for items like sportswear, socks, underwear and towels, where odor control is very important.
Bamboo fiber is popular for items like socks and hats because it quickly wicks away moisture and dries faster than other materials, making it ideal for managing high perspiration levels.
4. Breathability
Bamboo fabric is highly breathable because of the unique hollow structure of bamboo fibers. This hollow structure allows air to circulate freely and helps to regulate body temperature.
The breathability of bamboo fabric also aids in moisture-wicking, drawing sweat away from the skin and allowing it to evaporate quickly.
This makes bamboo an ideal clothing material, particularly in activewear and sportswear, where maintaining comfort and dryness is very important.
5. UV Protection
Bamboo fabric naturally provides a UPF 50+ rating, offering outstanding protection against both UVA and UVB rays. This means it effectively blocks out approximately 98% of harmful UV radiation, helping to safeguard your skin during the summer and outdoor activities.
Additionally, studies have shown that bamboo fabric has lower reflectivity compared to other materials like flax and cotton, making it effective at absorbing UV radiation.
Sodium copper chlorophyllin in bamboo fiber is notable for its UV absorption capacity, which is significantly higher—up to twenty times—than that of cotton fiber.
The density of bamboo fibers is crucial for blocking UV rays, as their tightly packed structure forms an effective barrier against harmful radiation.
This ability to block ultraviolet rays makes bamboo an ideal choice for summer clothing, especially for protecting pregnant women and children.
6. Durability and Longevity
Due to remarkable tensile strength of bamboo fibers, fabric is well-known for its durability and longevity.
These fibers are incredibly strong, making the fabric resistant to wear and tear, even with frequent use and washing.
Bamboo’s natural strength ensures that garments and products made from it maintain their shape and integrity over time. You can see clear difference between bamboo t-shirt and cotton t-shirt. Bamboo cloth is said to last three times longer than cotton.
This resilience makes bamboo an excellent choice for a wide range of applications, from everyday clothing to heavy-duty items, offering long-lasting performance and value.
7. Biodegradability
Unlike synthetic materials, bamboo fibers break down naturally and decompose without releasing harmful chemicals into the environment.
This environmentally sustainable property ensures that bamboo products have a minimal carbon footprint, contributing to reduced waste and reduce the impact on landfills.
Choosing bamboo fabric supports a more sustainable lifestyle and promotes the health of our planet.
Bamboo and bamboo fabric offer numerous environmental and human health benefits, particularly in terms of sustainable cultivation and the inherent properties of bamboo fibers.
Bamboo Clothing Products
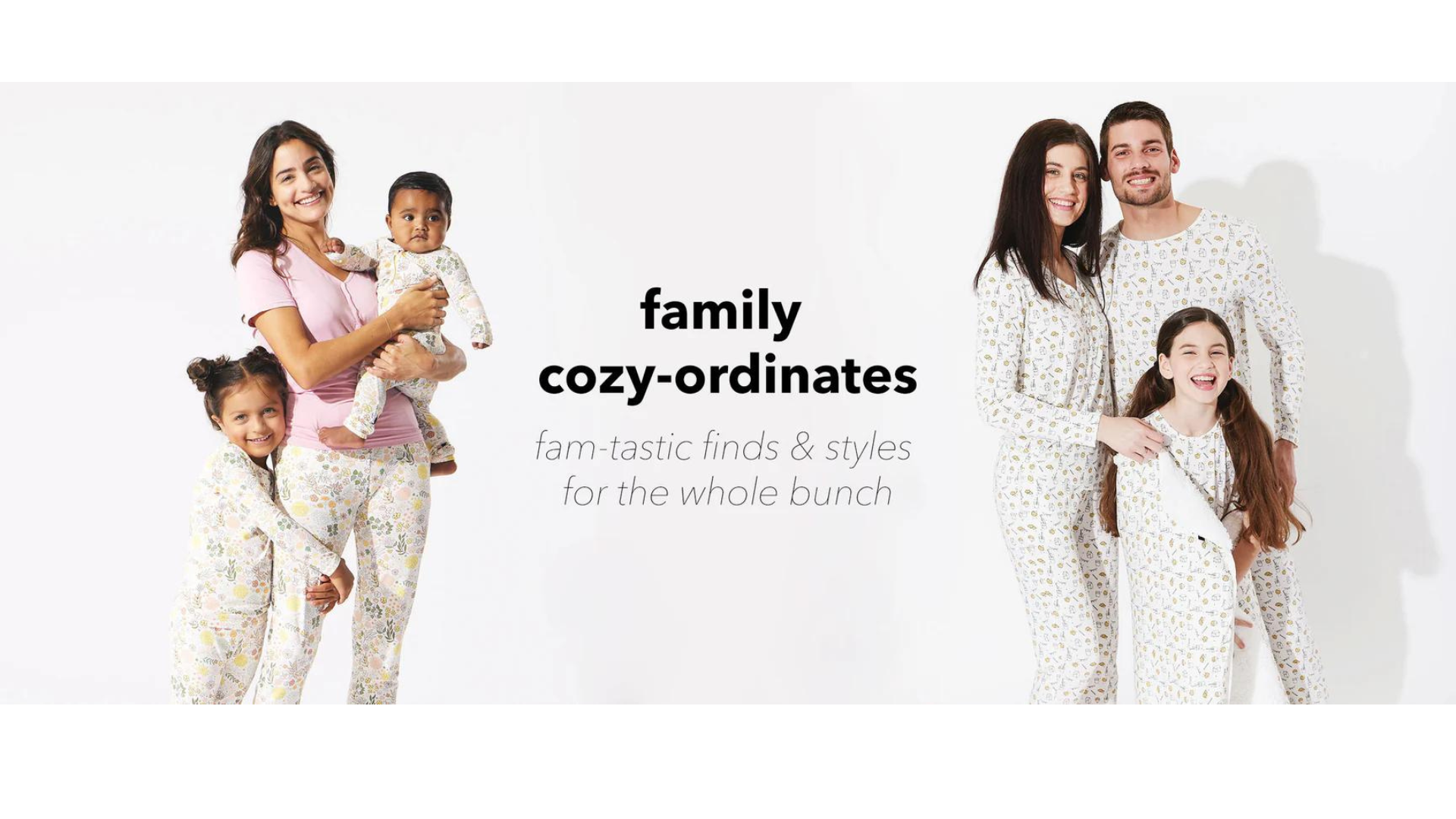
Bamboo clothing materials are versatile and cater to various age groups due to their softness, comfort, antibacterial and hypoallergenic properties.
Bamboo Baby Clothing
Onesies and Bodysuits: Soft and gentle on sensitive skin, suitable for newborns and infants.
Pajamas and Sleepwear: Breathable and moisture-wicking, keeping babies comfortable during sleep.
Tops and Bottoms: Lightweight and stretchy, ideal for active toddlers.
Socks and Accessories: Hypoallergenic and antibacterial, reducing irritation and allergies.
Bamboo Clothing for Adults
T-Shirts and Tank Tops: Soft, breathable, and suitable for everyday wear.
Leggings and Pants: Stretchy and comfortable, offering ease of movement.
Dresses and Skirts: Elegant and lightweight, perfect for warmer weather.
Sports Bras and Tops: Moisture-wicking and supportive, ideal for workouts.
Athletic Shorts and Pants: Flexible and quick-drying, enhancing performance during exercise.
Pajamas and Nightgowns: Soft, cozy, and temperature-regulating, promoting restful sleep.
Robes: Luxurious and comfortable, providing warmth and relaxation.
Underwear: Breathable, moisture-wicking, and hypoallergenic, offering comfort all day.
Socks: Antibacterial and odor-resistant, keeping feet dry and fresh.
How to Ensure Bamboo Fabric is Really Sustainable?
In the late 2000s, textile manufacturers, particularly in an online marketplace, heavily marketed bamboo fabrics, claiming luxurious softness, deeper colors than cotton, exceptional UV protection, and natural antimicrobial properties. These claims were backed by assertions of eco-friendly bamboo cultivation.
To verify these, government authorities and researchers globally investigated the true nature of the bamboo in these garments and found that the fibers closely resembled conventional viscose rayon, not genuine bamboo fibers.
Moreover, the samples showed no antimicrobial properties, confirming that the fibers were a type of rayon, not authentic bamboo. So, it is more crucial to ensure sustainability of clothing fabrics before purchasing any apparel.
Here’s a detailed approach:
1. Look for Certified Products
Various certifications and standards have been established for bamboo textiles to ensure they meet criteria for environmental sustainability, ethical sourcing, and quality.
OEKO-TEX Standard 100
Ensures that the fabric has not used toxic chemical during its manufacturing.
It tests fabrics before declaring them safe for human use.
Global Organic Textile Standard (GOTS)
It is especially applicable for organic textiles and ensures environmentally and socially responsible manufacturing.
Forest Stewardship Council (FSC)
Ensures that the bamboo or raw material comes from responsibly managed forests that provide environmental, social, and economic benefits.
Cradle to Cradle
Certifies products that are safe, circular, and responsibly made.
It is focusing on material health, reutilization, renewable energy, water stewardship, and social fairness.
2. Research the Manufacturer
Check the manufacturers’ practices for ensuring their sustainable and ethical standards:
Transparency
Look for brands that are transparent about their supply chain, including sourcing, processing, and labor practices.
Sustainable Practices
Check if the manufacturer uses closed-loop processes for chemical processing. Closed-loop processes help to minimize environmental impact.
Worker Rights
Ensure that the manufacturer follows the principle of fair trade to provide safe working conditions, fair wages, and respect workers’ rights.
3. Understand the Processing Methods
Understanding the different methods of bamboo processing can help assess their sustainability:
Mechanical Processing
Prefer brands that use mechanical processing methods, as they are generally more environmentally friendly.
Closed-Loop Chemical Processing
If chemical processing is used, ensure that the manufacturer employs a closed-loop system to recycle and reuse chemicals, significantly reducing waste and environmental impact.
4. Evaluate Environmental Impact Statements
Some brands and manufacturers provide environmental impact statements or reports that detail their sustainability practices. Look for:
Life Cycle Assessments (LCA)
Reports that evaluate the environmental impact of a product throughout its life cycle.
6. Consumer Reviews and Third-Party Audits
Look for reviews and audits from third-party organizations and consumer watchdogs:
Consumer Reviews
Check reviews from other consumers who have assessed the sustainability claims of the brand.
Third-Party Audits
Seek out third-party audits or evaluations from independent organizations that specialize in assessing environmental and ethical standards in manufacturing.
Top 5 Bamboo Clothing Brands
Here are five leading bamboo fabric manufacturers known for their commitment to sustainability and high-quality products:
1. Litrax (LITRAX – Innovative Fibers & Yarn) – Switzerland
Litrax is well known for its innovation in bamboo fiber technology.
The company is committed for sustainable practices, utilizing closed-loop systems in their manufacturing processes to minimize environmental impact.
2. Shanghai Tenbro Bamboo Textile Co., Ltd. – China
Shanghai Tenbro is a leading manufacturer of bamboo fiber and bamboo fabric.
The company is recognized for its extensive research and development in sustainable bamboo processing technologies.
3. China Bambro Textile Company Limited – China
China Bambro is another major player in the bamboo textile industry.
The company focuses on producing high-quality bamboo yarn and fabric, emphasizing sustainable and eco-friendly practices.
They utilize advanced technology to ensure their products meet international environmental and quality standards.
4. TexereSilk – USA
TexereSilk is known for its luxurious bamboo textiles, including clothing, bedding, and bath products.
The company places a strong emphasis on sustainability, using eco-friendly dyes and processing methods.
TexereSilk’s bamboo products are certified by various international standards, ensuring their commitment to environmental responsibility.
5. Greenyarn – USA
Greenyarn is a pioneer in producing eco-friendly bamboo fabrics.
They specialize in developing advanced bamboo nanotechnology fabrics that are not only sustainable but also offer enhanced antibacterial and antifungal properties.
Greenyarn’s products are designed for a variety of applications, including clothing, medical textiles, and home goods.
These manufacturers are leading the way in the bamboo fabric industry, combining innovation, quality, and sustainability. By focusing on eco-friendly practices and advanced technologies, they are setting high standards for the production of bamboo textiles and contributing to a more sustainable future in the fashion and textile industry.
Conclusion
In the face of climate change and global warming, making sustainable fashion choices is vital for reducing the environmental footprint of the fashion industry. By opting for eco-friendly materials, conserving water, minimizing chemical use, and promoting ethical practices, the fashion sector can play a significant role in combating environmental degradation and fostering a more sustainable future. Sustainable fashion not only benefits the planet but also supports healthier ecosystems and more equitable societies.