In search of sustainable and eco-friendly materials, wheat straw plastic pop-up as a promising alternative to petroleum-based plastic. With growing environmental concerns and the push for reducing plastic pollution, wheat straw plastic offers a potential solution to mitigate plastic pollution and its negative consequences.
Rising awareness among the consumers and manufacturers for the environmental impact of plastic waste has fueled demand for biodegradable and compostable materials like wheat straw plastic.
Additionally, regulatory pressures continue to drive demand for sustainable solutions, where wheat straw plastic plays a crucial role in promoting a more sustainable and circular economy. Continued research, innovation, and collaboration will further enhance its benefits and expand its applications across various industries globally.
Table of Contents
Introduction
Plastic pollution has become a global problem and posing a significant threat to our ecosystems.
From the depths of the oceans to the highest peaks of the mountains, plastic waste is everywhere on our blue planet.
Currently, plastic manufacturing and its use is at its highest peak, but the recycling rate for plastics is only 10%, which is very low.
So as a result, the rest of plastics either gets incinerated or finds its way into the environment.
Negative Environmental Impact of Petroleum-based Plastics
Non-Biodegradability
Petroleum-based plastics can take hundreds to thousands of years to decompose. During this time, they accumulate in landfills and contribute to long-term environmental pollution and degradation.
Microplastic Pollution
Petroleum-based plastics are never degraded fully, instead they break down into smaller fragments or micro-plastics, which contaminate soil, groundwater and ocean.
These tiny particles are ingested by wildlife, entering the food chain and posing health risks to animals and humans over the time.
Ocean Pollution
7-8 million tons of plastic enter the ocean every year, which form massive garbage patches, like the Great Pacific Garbage Patch.
Marine animals ingest or become entangled in plastic debris, leading to injury, starvation, and sometimes death.
Greenhouse Gas Emissions
The production, transportation, and disposal of plastics generate significant amounts of greenhouse gases, contributing to climate change.
The incineration of plastic waste also releases toxic fumes and CO2.
Toxicity
Even though we are aware of the deadly impacts of plastic, we are still using it in our daily life.
Plastics contain plasticizers or additives like phthalates, BPA, and flame retardants, which can leach into the environment and pose health risks to humans and wildlife.
These toxic chemicals are linked to various health issues, including hormonal disruptions and cancer.
As environmental issues are growing day by day, the need for sustainable alternatives to traditional petroleum-based plastics is more important. Bioplastics, made from renewable resources, has emerged as a promising solution.
What are Bioplastics?
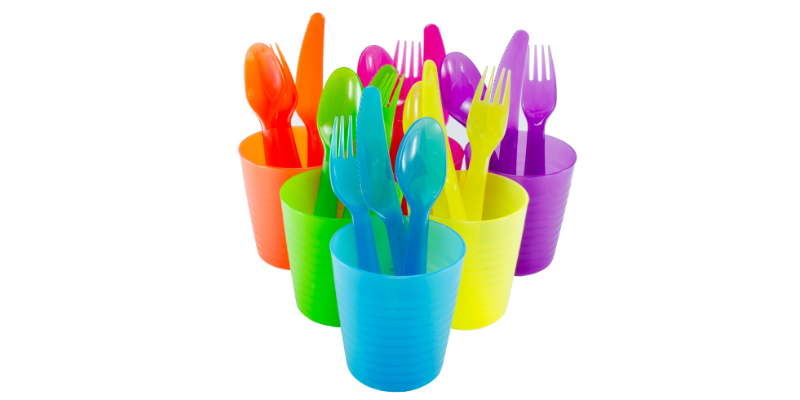
Bioplastics are a category of plastics derived from biological sources such as plants, agricultural byproducts, and other renewable materials. Unlike traditional plastics, which are synthesized from finite fossil fuels, bioplastics aim to minimize carbon footprint and promote sustainability throughout their lifecycle.
They can be biodegradable or compostable, further mitigating environmental pollution.
Types of Bioplastics
- Wheat Straw Plastic
- Corn Starch Plastic
- Sugarcane Bagasse
- Other Innovative Bioplastics
Bioplastics, including wheat straw plastic, corn starch plastic, sugarcane bagasse, and other innovative materials, represent a crucial step towards a more sustainable and environmentally friendly future.
What is Wheat Straw Plastic?
Wheat straw plastic is a type of bioplastic made from the leftover stalks of wheat plants after the grain has been harvested. These stalks, typically considered agricultural waste, are repurposed and combined with biodegradable polymers like PLA (polylactic acid) to create a durable and versatile material.
This innovative use of wheat straw not only diverts waste from landfills but also reduces the reliance on petroleum-based plastics.
Traditional Disposal Methods for Wheat Straw
Wheat is a major crop grown globally, especially in regions like North America, Europe, Asia, and Australia. The extensive cultivation of wheat results in the generation of large quantities of straw annually.
Traditionally, wheat straw was either burned or left to decompose naturally, contributing to environmental issues such as air pollution and inefficient land use.
Burning
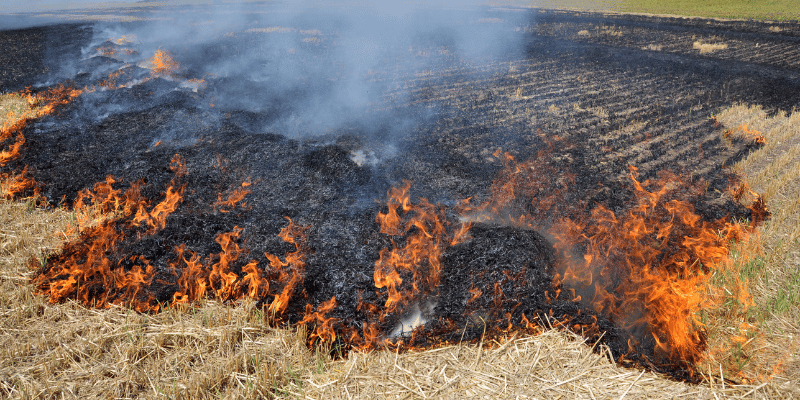
In many regions, wheat straw is often burned in the fields to clear the land for the next planting season.
This practice releases huge amounts of carbon dioxide, particulate matter, and other pollutants into the atmosphere, contributing to air pollution and climate change.
Landfill
When wheat straw is disposed of in landfills, it can produce methane gas as it decomposes without oxygen.
In summary, wheat straw plastic is a bioplastic or plant-based plastic derived from the stalks of wheat plants and combined with biodegradable polymers. It offers a sustainable and environmentally friendly alternative to conventional plastics.
Its use helps to mitigate plastic pollution, reduce carbon emissions, and promote the efficient utilization of agricultural waste.
Manufacturing Process of Wheat Straw Plastic
The manufacturing process of wheat straw plastic can be carried out in two distinct ways:
- 1. Extracting Cellulose from Wheat Straw
- 2. Blending Wheat Straw Fiber with PLA (Polylactic Acid)
Extracting Cellulose from Wheat Straw
The manufacturing procedure for extracting cellulose from wheat straw and creating wheat straw plastic involves a series of steps, from initial cleaning and grinding to chemical treatment, drying, and finally molding and shaping into usable products.
1. Collection and Preparation
Wheat straw is collected from agricultural fields after the wheat grains have been harvested. The straw is then cleaned with water and chopped into smaller pieces.
2. Grinding
The chopped wheat straw is crushed into a fine powder to create a uniform raw material for plastic production.
3. Chemical Treatment
Alkali Treatment: Mix the straw powder with a solution of sodium hydroxide (NaOH) and heat the mixture at around 90-100°C for 1-2 hours to break down lignin and hemicellulose.
Separation: Filter the mixture to separate the solid cellulose from the liquid containing dissolved lignin and hemicellulose.
Wash the solid cellulose with water to remove any residual chemicals.
4. Bleaching (Optional for Purity)
Bleaching Agent: Treat the washed cellulose with a bleaching agent, such as hydrogen peroxide (H₂O₂) to achieve a higher purity level.
Neutralization: After bleaching, neutralize the cellulose with an acid (e.g., acetic acid) to remove any remaining alkali residues.
Final Washing: Rinse the cellulose thoroughly with water to ensure all chemicals are removed.
5. Drying
Dehydration: Remove excess water from the washed cellulose using mechanical pressing or centrifugation.
Drying: Air-dry or oven-dry the cellulose at a controlled temperature (60-70°C) to achieve a consistent moisture content.
6. Formulation of Wheat Straw Plastic
Polymerization: The extracted cellulose undergoes a polymerization process where the cellulose molecules bond together, creating long chains that are typical of plastic materials.
Cellulose itself cannot be directly polymerized into plastic in its natural state due to its crystalline structure. However, cellulose can be chemically modified to create derivatives that can be processed into plastic materials. Common cellulose derivatives, such as cellulose acetate, cellulose nitrate, cellulose ethers etc.
7. Molding and Shaping
After polymerization, mold the plastic granules into the desired shapes, such as containers, cutlery, or other plastic products.
Control the molding temperature and pressure to ensure proper fusion and shaping of the bioplastic material.
8. Cooling and Finishing
Cooling: Allow the molded products to cool and solidify in the molds.
Finishing: Perform any necessary finishing operations, such as trimming excess material, smoothing edges, and inspecting for defects.
Blending Wheat Straw Fiber with PLA (Polylactic Acid)
In this type of manufacturing process, wheat straw is combined with biodegradable polymers like PLA, which is derived from corn starch or sugarcane. Addition of biopolymer or PLA into wheat straw fiber increases the functional properties of resulting materials.
1. Collection and Preparation
Wheat straw is collected from agricultural fields after the wheat grains have been harvested. The straw is then cleaned with water and chopped into smaller pieces.
2. Grinding
The chopped wheat straw is crushed into a fine powder to create a uniform raw material for plastic production.
3. Mixing with Biodegradable Polymers
This wheat straw powder is mixed with biodegradable polymers. The mixing process ensures that the natural fibers are evenly distributed throughout the biopolymer matrix to achieve the desired strength and durability.
4. Extrusion
The mixture is fed into an extruder, where it is heated and melted to form a homogeneous blend. The molten material is then shaped into pellets or granules.
5. Molding
The pellets or granules are used in various molding processes, such as injection molding or extrusion molding, to create different products.
These products can range from cutlery and tableware to packaging materials and more.
Composition of Wheat Straw Plastic
The composition typically includes the following components:
1. Wheat Straw
Cellulose: This is the primary component of wheat straw, cellulose provides strength and rigidity. It constitutes about 30-45% of the straw’s weight.
Hemicellulose: This polysaccharide acts as a filler and binding agent, making up 20-30% of the straw’s weight.
Lignin: Lignin provides structural support and resistance to microbial degradation, accounting for about 15-25% of the straw.
Silica and Other Minerals: Wheat straw contains small amounts of silica (5-10%) and other minerals, which can enhance the material’s mechanical properties.
2. Polylactic Acid (PLA)
Polylactic Acid (PLA): PLA is a biodegradable and bioactive thermoplastic, derived from renewable resources like corn starch or sugarcane.
It is used to bind the wheat straw fibers to enhance the plastic’s overall properties.
PLA constitutes a significant portion of the bioplastic blend, usually around 50-70%.
3. Additives and Plasticizers
Plasticizers: They are added to improve the flexibility and processability of the bioplastic. Common plasticizers include glycerol, citrate esters, and polyols.
Coupling Agents: They agents are used to enhance the adhesion between the wheat straw fibers and the PLA matrix. Maleic anhydride or silane compounds are commonly used coupling agents.
Fillers: Additional fillers, such as calcium carbonate or talc, may be incorporated to improve mechanical properties, reduce cost, and enhance the bioplastic’s stability.
Colorants and UV Stabilizers
Colorants are used to provide color, while UV stabilizers are used to protect the material from UV degradation. This is very useful when plastic materials are under exposure to direct sunlight.
Proportions and Blending
The exact proportions of these components can vary depending on the desired properties of the final product. A typical formulation might look like this:
Wheat Straw Fiber: 20-40%
PLA: 50-70%
Additives and Plasticizers: 5-10%
Direct Molding of Wheat Straw Fibers
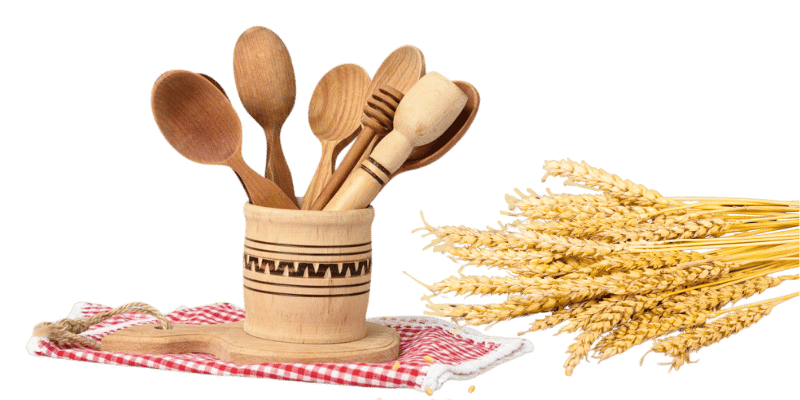
Additionally, wheat straw fiber can be molded directly into various shapes and forms, making it suitable for various applications ranging from food containers, utensils and household items.
1. Collection and Preparation
Wheat straw is collected from agricultural fields after the wheat grains have been harvested. The straw is then cleaned with water and chopped into smaller pieces.
2. Grinding
The chopped wheat straw is crushed into a fine powder to create a uniform raw material for plastic production.
3. Binding and Pre-treatment
Mixing with Binders: Combine the wheat straw fibers with natural binders (e.g., starch, cellulose derivatives) or biodegradable resins to enhance strength and moldability.
Pre-treatment: Pre-treat the fiber-binder mixture with steam or mild chemical treatments to make the fibers more pliable and improve binding.
4. Molding Process
A. Compression Molding
1. Preparation:
Preheat the mold to the desired temperature (typically 160-180°C).
Measure and place the appropriate amount of wheat straw fiber mixture into the mold cavity.
2. Compression:
Close the mold and apply pressure using a hydraulic press.
Maintain the pressure (ranging from 50 to 200 psi) and temperature for a specified time (usually 5-10 minutes) to allow the fibers to bond and shape into the mold.
3. Cooling:
Gradually release the pressure and allow the molded product to cool in the mold to solidify its shape.
Open the mold and remove the finished product.
B. Injection Molding (for Blended Composites)
1. Preparation:
Use wheat straw fiber mixture.
Preheat the injection molding machine to the appropriate temperature for the biopolymer (typically 180-220°C).
2. Injection:
Feed the wheat straw fiber mixture into the injection molding machine.
The machine melts the material and injects it into the mold cavity under high pressure.
3. Cooling and Ejection:
Allow the mold to cool, solidifying the molded product.
Open the mold and eject the finished product.
5. Finishing
Trimming: Remove any excess material or flash from the molded product using trimming tools.
Smoothing: Smooth the edges and surfaces as needed to ensure a high-quality finish.
Inspection: Inspect the products for any defects or inconsistencies.
Applications of Wheat Straw Plastic
Wheat straw plastic, a sustainable plant-based material derived from agricultural waste, finds diverse applications across several industries due to its biodegradability, renewable sourcing, and potential to reduce environmental impact.
Here’s how wheat straw plastic is utilized in various sectors:
1. Food Packaging
Wheat straw plastic is gaining popularity as a packaging material for food products due to its biodegradability and compostability.
Biodegradable Food Containers: Wheat straw plastic is used to manufacture biodegradable food containers and packaging trays.
These containers are suitable for takeaway meals, salads, and other food items, offering an eco-friendly option to reduce plastic waste.
Disposable Cutlery: Biodegradable forks, spoons, and knives made from wheat straw plastic are increasingly used in fast-food chains, restaurants, and catering services, providing a sustainable alternative to single-use plastic cutlery.
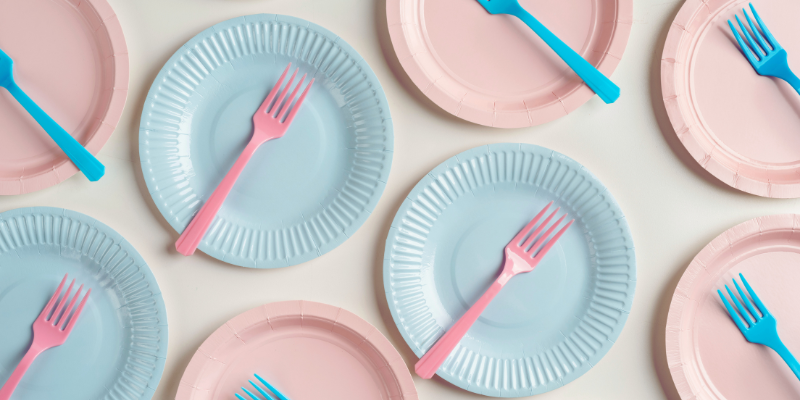
Wheat straw plastic is generally considered safe by the FDA for food contact applications, additionally it is gluten-free, BPA-free, and does not leach harmful chemicals or toxins into food.
2. Consumer Goods
Cosmetic Packaging: Wheat straw plastic is utilized in the production of biodegradable containers and tubes for cosmetics and personal care products.
Compared to some conventional plastics, which may contain BPA or phthalates, wheat straw plastic free from such toxic chemicals and provides a safer option for food and cosmetic packaging.
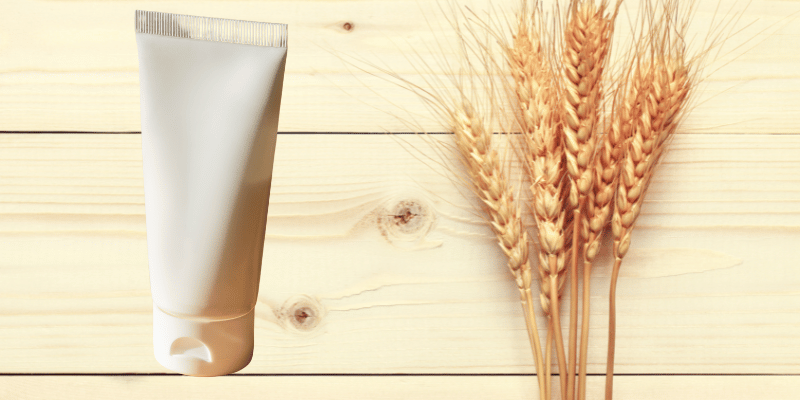
Household Items: Manufacturers produce a range of household items using wheat straw plastic and wheat straw molding fibers, including storage containers, plates, cutting boards, and kitchen utensils.
These products offer durability and functionality while supporting eco-friendly lifestyles.
Electronics Accessories: Wheat straw plastic is employed for producing phone cases, laptop sleeves, and other electronic accessories.
3. Agricultural Products
Biodegradable Plant Pots and Seedling Trays: Wheat straw plastic is used in the manufacturing of biodegradable plant pots and seedling trays for nurseries and gardening.
These products help to reduce plastic waste in horticultural applications while promoting sustainable gardening practices.
Biodegradable Mulch Films: Biodegradable mulch films made from wheat straw plastic are used in agriculture for weed control, moisture retention, and soil health improvement.
These films degrade naturally and enrich the soil, while reducing environmental impact compared to petroleum-based plastics.
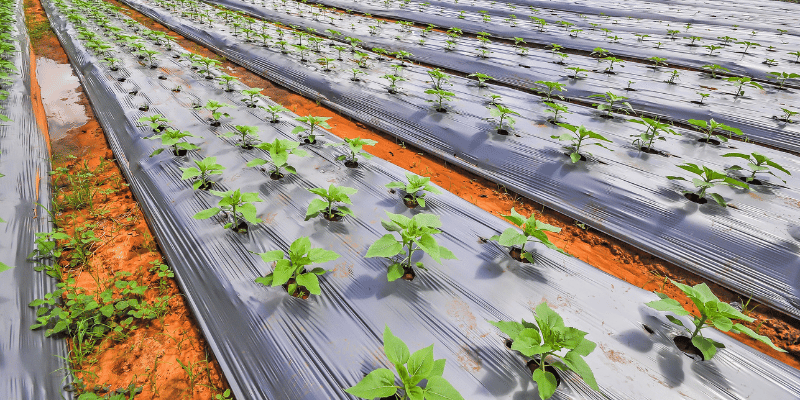
4. Automotive Industry
Wheat straw plastic is implemented in automotive industries for manufacturing components such as door panels, dashboard trims, and storage compartments.
Its lightweight properties and sustainability benefits make it attractive for reducing vehicle weight and environmental impact.
5. Building Materials
Straw is used in the production of eco-friendly building materials, such as straw bales for thermal insulation and strawboard for construction panels (Bio composite panels).
6. Paper and Packaging
The cellulose content in wheat straw makes it suitable for producing paper and packaging materials, reducing the reliance on wood or timber pulp.
Advantages of Wheat Straw Plastic
Wheat straw plastic offers numerous advantages for both humans and the environment, making it an attractive alternative to traditional plastics.
Here’s a detailed look at its benefits:
Biodegradability
One of the most significant advantages of wheat straw plastic is its ability to biodegrade naturally, reducing the environmental impact compared to traditional plastics.
Many bioplastics are designed to compost naturally or through industrial composting facilities to reduce plastic pollution.
The EN13432 certification guarantees that a product can break down in industrial composting facilities, converting into carbon dioxide, water, and biomass within a specified period.
Consumers, which are looking for biodegradable products should look for this certification or similar endorsements.
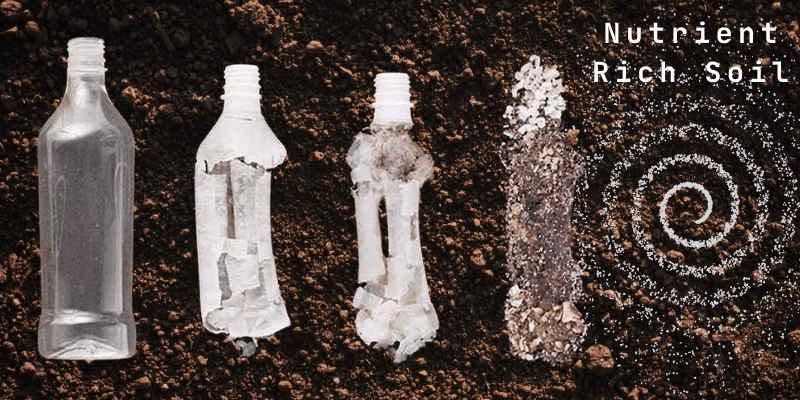
Renewable Resource
Wheat straw is an abundant agricultural byproduct, making it a readily available and renewable resource for bioplastic production.
Bioplastics, which are made from renewable plant-based materials, can reduce dependency on limited fossil fuels.
Reduced Carbon Footprint
The production of wheat straw plastic typically involves lower carbon emissions compared to petroleum-based plastics. Using wheat straw instead of burning it is the best way to reduce carbon emissions.
Non-Toxic
Wheat straw plastic is generally free from harmful chemicals and toxins, making it safer for both human health and the environment. It is approved by the FDA and can be used in food and cosmetics packaging.
Durability
When combined with other biodegradable polymers, such as polylactic acid (PLA) and polyhydroxyalkanoates (PHA), wheat straw plastic exhibits excellent mechanical properties, making it suitable for various applications.
Reduction in Plastic Waste
By using wheat straw as a raw material, industries can reduce their reliance on fossil fuels used in the production of traditional plastics.
Furthermore, it also helps to reduce the accumulation of plastic waste in landfills and oceans.
Waste Utilization
Wheat straw plastic utilizes agricultural byproducts that would otherwise be burned or disposed of, promoting a circular economy and contributing to more efficient resource use.
It transforms agricultural waste into valuable products, creating additional income source for the farmers.
Disadvantages of Wheat Straw Plastic
While wheat straw plastic offers several environmental and human health benefits, it also comes with certain disadvantages and challenges that need to be addressed.
Cost of Production
The production of wheat straw plastic can be more expensive than conventional plastics due to the unavailability of infrastructure, low volume, additional processing steps and the cost of biodegradable polymers, although economies of scale and technological advancements are gradually improving cost-effectiveness in the future.
Limited Heat Resistance
Wheat straw plastic may have lower heat resistance compared to some conventional plastics, limiting its suitability for high-temperature applications like hot food containers and microwave use.
Moisture Sensitivity
Wheat straw fibers are hygroscopic in nature and can absorb moisture over time, potentially affecting the integrity and durability of the plastic in humid or wet environments.
Performance Variability
The quality and performance of wheat straw plastic can vary depending on the source and processing of the raw materials.
Wheat straw is derived from wheat plants (Triticum species), one of the most widely cultivated cereal crops globally.
Infrastructure Requirements
The widespread adoption of wheat straw plastic requires investment in new infrastructure and technologies for collection, processing, and recycling.
Infrastructure Challenges: Limited infrastructure and facilities for composting or recycling of bioplastics, like wheat straw plastic may hinder widespread adoption.
Contamination: Mixing of biodegradable plastics with conventional plastics in recycling streams can contaminate recycling process and reduce overall recyclability.
Durability Concerns
Mechanical Strength: Wheat straw plastic may still have lower mechanical strength and durability compared to traditional plastics in certain applications.
Longevity: Products made from wheat straw plastic may have a shorter lifespan in terms of wear and tear compared to petroleum-based plastic.
Competing Uses
The demand for wheat straw as a raw material for bioplastics may compete with its use for other purposes, such as animal bedding, soil enrichment, or biofuel production.
Regulatory Frameworks
Standards and Certifications: Compliance with evolving regulatory standards and certifications for bioplastics can be complex and require ongoing investment in research and development.
Future Outlook in Wheat Straw Plastic
Ongoing research and development (R&D) for wheat straw plastic focuses on enhancing its properties, expanding applications, improving sustainability metrics, and overcoming existing challenges.
Here are key areas of current R&D efforts:
Material Properties Enhancement
Mechanical Strength: Improving the mechanical properties of wheat straw plastic, such as tensile strength and impact resistance, to match with those of traditional plastics.
Durability: Enhancing durability and dimensional stability to ensure longevity in various applications, including packaging, consumer goods, and automotive components.
Heat Resistance: Developing formulations that withstand higher temperatures, expanding the range of applications in hot climates or for products requiring heat resistance.
Processing and Manufacturing Innovations
Efficiency Improvements: Optimizing processing techniques for converting wheat straw into usable fibers or particles, reducing energy consumption and production costs.
Compatibility: Investigating compatibility with existing manufacturing equipment and processes to facilitate scalability and integration into existing supply chains.
Formulation Development: Experimenting with different ratios of wheat straw fibers and biodegradable polymers to achieve optimal material properties and performance characteristics.
Environmental Impact Reduction
Lifecycle Assessment: Conducting comprehensive LCAs to quantify environmental benefits and identify areas for further improvement in carbon footprint, resource use, and waste reduction.
Biodegradation Studies: Studying the biodegradation behavior of wheat straw plastic in various environments to optimize compostability and end-of-life disposal options.
Toxicity Assessments: Evaluating potential environmental and human health impacts of additives and degradation products to ensure safety and regulatory compliance.
Novel Applications
Exploring innovative applications for wheat straw plastic in sectors beyond traditional packaging and consumer goods, such as construction materials, textiles, and medical devices.
Disposable Medical Devices: Wheat straw plastic may find applications in single-use medical devices and packaging. Its biocompatibility and potential for sterile applications make it suitable for certain healthcare products.
Biodegradable Fibers: Research is underway to develop biodegradable fibers and textiles from wheat straw plastic. These materials offer potential applications in clothing, footwear, and textiles, contributing to the sustainability goals of the fashion industry.
Biodegradable Films and Coatings
Advances in wheat straw plastic formulations are enabling the development of biodegradable films and coatings for food packaging and agricultural applications.
These materials offer moisture resistance and barrier properties while reducing plastic waste.
Conclusion
Wheat straw plastic represents a step forward in the journey towards sustainable and eco-friendly materials. By repurposing agricultural waste and reducing reliance on petroleum-based plastics, this bioplastic offers a promising solution to the plastic pollution crisis. While there are challenges to overcome, such as cost and performance variability, the potential benefits of wheat straw plastic in reducing environmental impact and promoting a circular economy are significant.
As technology advances and more industries adopt sustainable practices, wheat straw plastic could play a crucial role in shaping a greener future.
Frequently Asked Questions
Yes, wheat straw plastic is safe and FDA-approved as a bioplastic, making it suitable for various applications, including food contact, as long as it meets safety standards.
Yes, wheat straw is gluten-free. The gluten protein is found in the grain of wheat, not in the straw, making wheat straw products safe for individuals with gluten sensitivities or celiac disease.
Wheat straw plastic tableware typically decomposes in a composting environment within 3 to 6 months. The exact decomposition time can vary depending on environmental conditions such as temperature, humidity, and the presence of microorganisms.
Yes, wheat straw products are safe for food use. They are made from natural, non-toxic materials and are free from harmful chemicals commonly found in traditional plastics, such as BPA and phthalate.
Yes, wheat straw tableware is designed to be durable and can be reused multiple times. It is also dishwasher safe, making it convenient for everyday use.
Yes, wheat straw tableware is an environmentally friendly alternative to traditional plastic tableware. It is biodegradable, compostable, and made from renewable agricultural byproducts, reducing waste and the reliance on fossil fuels.
Do you know of any suppliers of this material in the UK, USA or Europe?
Yes, we do. Please leave your query on our Contact Us page with your requirements and location, and we’ll share the nearest supplier details if possible.